WELL HEAD / X-MASS TREE INSTALLATION & MAINTENANCE

4.1) INSPECTION & TECHNICAL SUPPORT FOR MAINTENANCE OF WELLHEAD & X-MASS TREE
- Inspection, installation and test of Wellhead and Christmas tree components on existing (work-over) and new (drilling) wells.
- Correct and fast flange make-up using bolt tensioning systems or torquing tools.
- Retrieving, disassembly and recovery of Christmas tree, Wellhead, valves and chokes from worked-over wells.
- Casing cold cut and beveling for the correct installation of Wellhead spools.
- Cold cut of casing spool for disengaging casing hanger
- Running/Retrieving and maintenance of drilling tools such as wear bushings, BOP test plugs, etc.
- Running/Retrieving and maintenance of Tubing and Annulus plugs such as Back Pressure Valve, Two Way Check Valve, VR plugs, etc. using lubricators.
- Welding of starting heads onto surface casing.
- Operation and maintenance of client supplied Wellhead tools.
- Leak off test of Wellhead and Xmas Tree valves and Subsurface safety valve
- Methanol, Brine and Glycol pumping services.
- Full field service capability with experienced engineers capable of carrying out equipment installation, testing and service both in the workshop and on location.
(4.2) CASING EXTERNAL/INTERNAL COLD CUTTERS
We are delighted to introduce our Split Frame Cold Cutting tools used mostly in cutting and preparing pipe end for wellhead installation and other fire field weld preparation. This is an integral aspect of the Well head services, but can be carried out as stand-alone service for Clients, who have such specific need.
In addition to eliminating the need for hazardous flame cutting, the cold cutting method enables operators to meet all potential requirements, both onshore and offshore.
Our cold cutting system produces a lathe-type beveled finish on casing ends without altering metallurgical properties. Cutting equipment quickly splits to mount to casing O.D. and requires minimal radial and axial clearance. The cold cutter can be set up and operational in less than
30 minutes. Stonewall cold cutters are portable, lightweight and compact, allowing for easy transport of equipment to tubular yards and to the wellsite.
(4.3) WELLHEAD INTEGRITY SURVEY & MANAGEMENT
Stonewall supports its customers in delivering hydrocarbons safely throughout the life of their wells, through smarter well integrity management, supported by a comprehensive range of well service, cased hole evaluation, well intervention and remedial services.
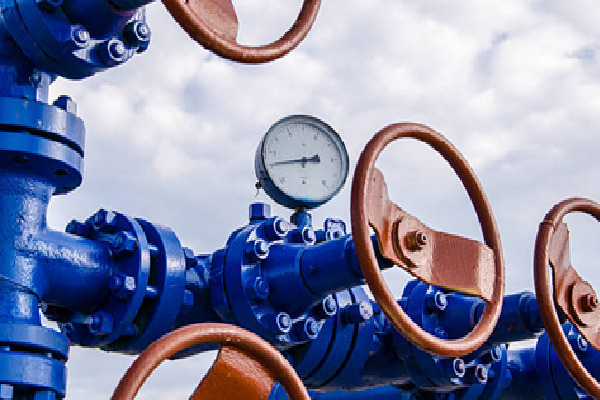
With a strong emphasis on preventative well integrity management systems, our consultants and engineers provide a highly responsive service to meet your full range of well integrity needs with clear objectives of maximizing well availability and productivity while minimizing regulatory and HSE risks.
Services provided ranges from assessment of existing well integrity management system; the design, implementation and management of a new well integrity management system; through to the planning and execution of any well site services required to assess or remediate your wells.
These capabilities are relevant throughout the entire well lifecycle, from initial design through to eventual abandonment.
Our Well integrity consulting and engineering team utilizes a well integrity management system that delivers well head integrity survey in the following areas:
- Well barrier, annulus and well integrity monitoring
- Tubing/casing caliper and thickness surveys
- Tubing/Annulus Integrity
- Tree and Well head Integrity
- Well Integrity Assessment and Management.
- ICP and Annulus investigation (bleed off, fill-up, monitoring)
- Wellhead pressure monitoring and maintenance using high sensitive instrument (Data Trap);
- Leak detection surveys and Downhole leak detection services
- Leak sealant injection for curing Wellhead packoff and hanger seals, Subsurface safety valves, Casing and Tubing packers, Wellhead valves, Microannular leaks (Seal-Tite).
- Downhole video and camera services
We have trained specialists to handle these services, which include but not limited to:
- Rig Condition Survey
- Rig Acceptance Testing
- BOP & Well Control Equipment( Surface & Subsurface) Inspection
- Dynamic Positioning Audit
- Complete Dropped Object Survey
- Risk Assessment, Facilitation & Management
- Audit & Commissioning Services.
- Statutory certifications for personnel & equipment
- Mast and Substructure inspection, including Dropped Objects Risks
- Rig equipment, drive motors and drawworks inspections
- Power generation, distribution equipment & SCR/Transformer inspection
- Mud pumps, drive motors and Compound drive arrangements.
- Drawworks and associated attachments
- High pressure mud systems
- Low pressure mud systems and treatment equipment
- Drill string package
- Safety equipment and implementation of system
- Maintenance system
- Spare parts
Key Areas of Services:
- Visual Body Inspection
- Visual Thread Inspection (VTI)
- API Full Length Drifting (FLD)
- Laser Tally Services
- Tubular Maintenance Programs
- Bevel, De-Dent and Straighten
- Bundling
- Coupling Bucking
- Decontamination Coating
- Dye Penetrant
- Electromagnetic Inspection (EMI) – two and four function
- Full-Length Ultrasonic Inspection
- Hydrostatic Testing
- Inspection and Bolstering of Chrome Tubing
- Magnetic Particle Inspection
- On-site Thread Cleaning and Visual Inspection (VTI)
- Scale and Paraffin Removal
- Special End Area (SEA) Inspection
- Third-Party Monitoring
- Thread Gauging
- Weld Line Ultrasonic Inspection
- Well Returns
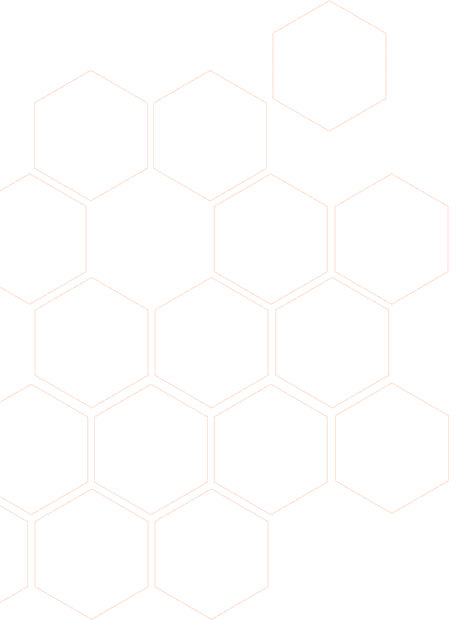
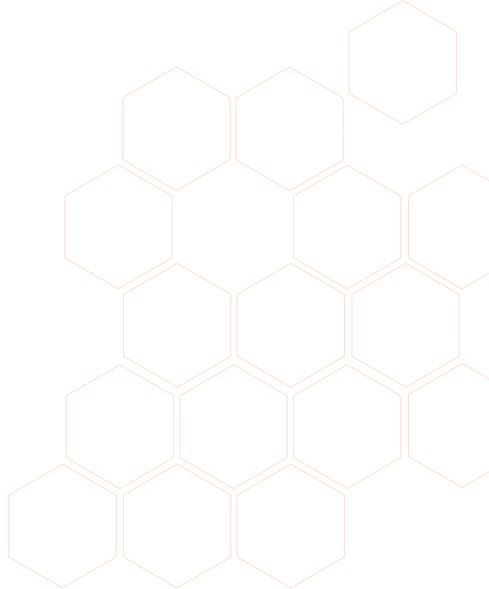
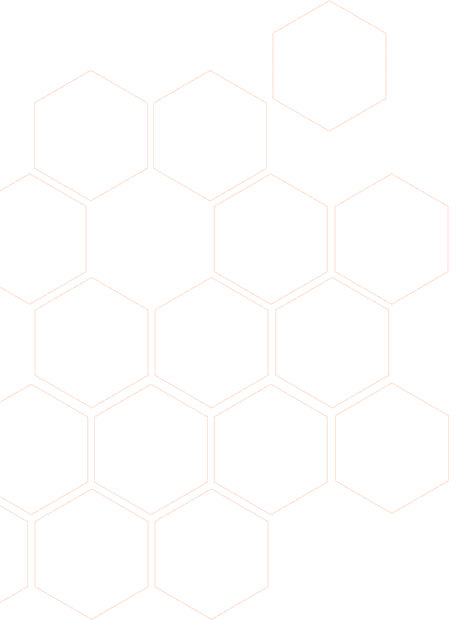
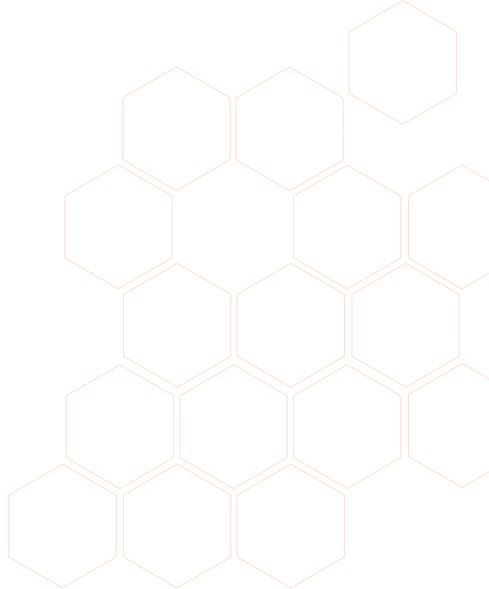